Overview
MyQ Warehouse is a three-part solution to tackle warehouse bottlenecks through innovative products that enhance productivity and efficiency for workers and truckers. I worked collaboratively with engineers, industrial and UX designers to create these three products from 0-1 in a span of 10 weeks through research, prototyping and development.
Objectives
Understand business and user challenges within the warehouse facility
Implement a system that is accessible for multiple users within the warehouse
Identify and analyze bottlenecks within the warehouse operations
Challenges
After interviewing staff and visiting the warehouse facility, we uncovered several challenges arising from the complex nature of warehouse operations.
01
Detention time outside docks costs facilities over $85 per hour in fees.
02
Warehouses commonly use Pick Ticket Management Systems (PKMS) to control inventory movement for receiving, picking, packing, and shipping. However, these tools become redundant when managers resort to whiteboards and dispatchers to communicate pallet visibility to truck drivers and warehouse workers. This reliance on manual methods results in bottlenecks.
03
Managers, warehouse workers, and truck drivers have distinct needs when handling incoming and outgoing orders
“How might we create a seamless ecosystem for better cross-communication for workers inside and outside of warehouse facility
Research and Discovery
After consulting with product managers and visiting the warehouse, we identified key factors affecting the supply chain industry. We observed that drivers, warehouse staff, and management are directly impacted by operational bottlenecks. We then assessed their goals and how our products could enhance their work in the warehouse setting.
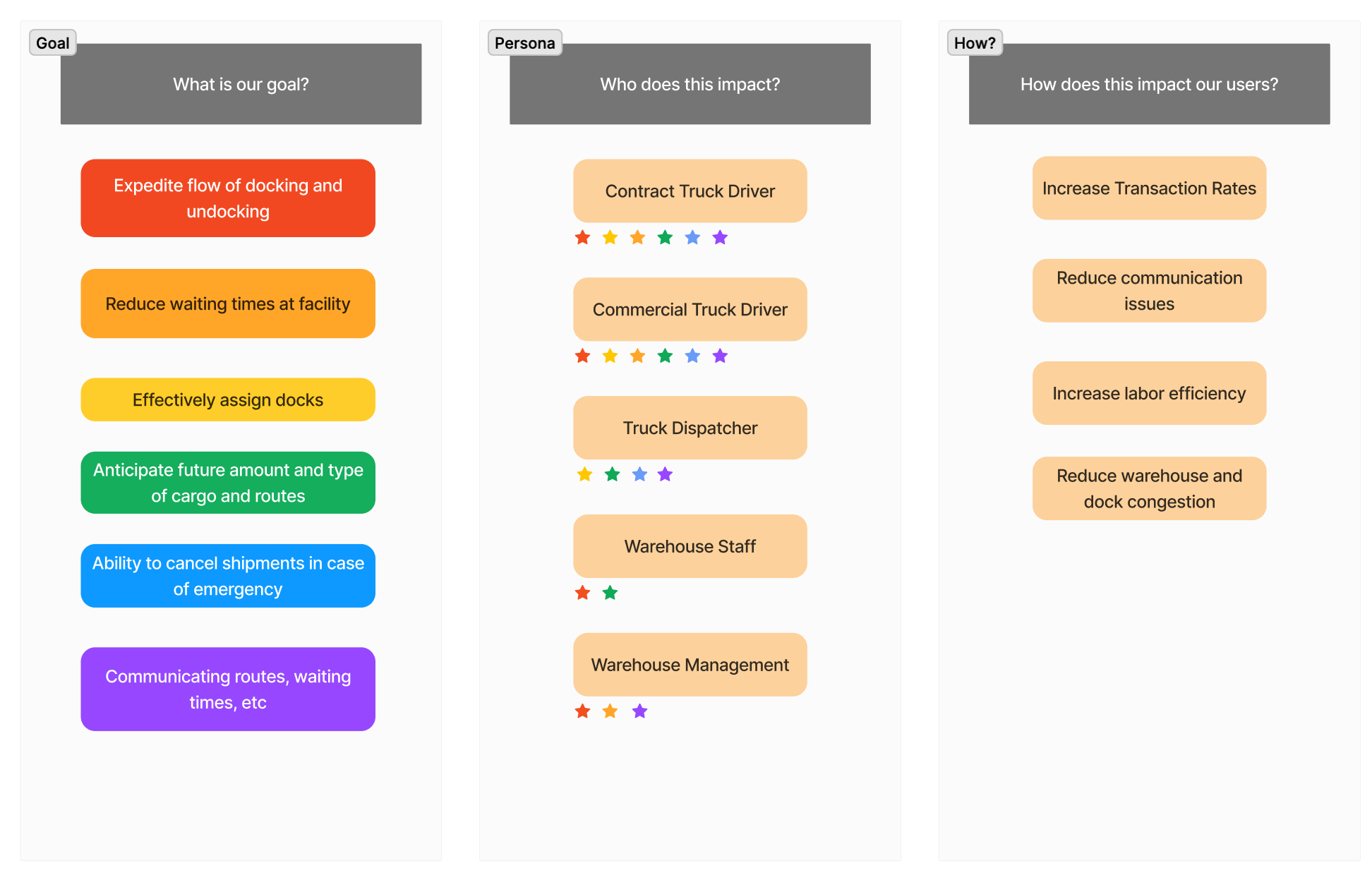
Insights & Recommendations
Insight 1
Complex warehouse systems for inbound and outbound deliveries result in bottlenecks and extended detention times. Consequently, warehouses incur costs by paying truck drivers for these detention periods.
Managers play a crucial role in ensuring that the facility and palettes are directed to the right places with minimal friction. They coordinate with dispatchers to provide dock codes to truck drivers, which can become challenging when hundreds of trucks are held at the facility without being docked. Docking is essential for the facility to load or unload palettes. If docks are not assigned efficiently and at appropriate times, the facility can become overwhelmed, forcing managers to pay detention fees to trucking companies and freelancers.
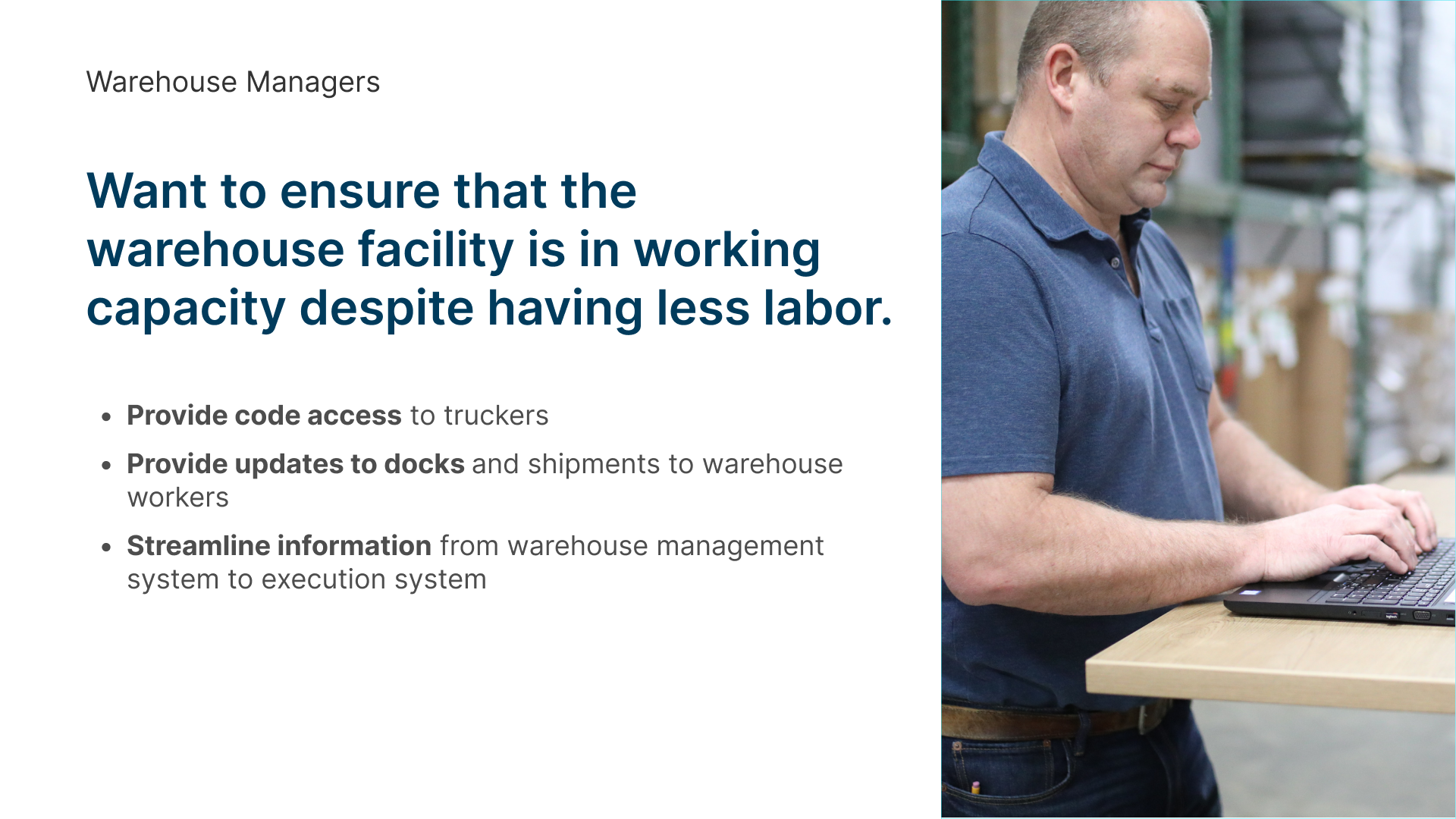
When evaluating the overall flow of the facility, we identified several key bottlenecks, highlighted in red. Miscommunication between dispatchers, truck drivers, and managers often leads to significant detention fees and creates congestion during the docking process. As a result, warehouse workers must rely on docking sensors to anticipate trucks at their dock. These sensors use a red-green light system to indicate whether a truck is successfully docked, but they do not provide information about the fulfillment status of the palettes within the truck. Additionally, warehouse workers rely on a manual whiteboard system maintained by managers to track the location of trucks in specific docks. This can lead to inefficiencies, as workers may spend time preparing to stage palettes for an incoming truck, only to find that a truck in detention needs their attention instead.
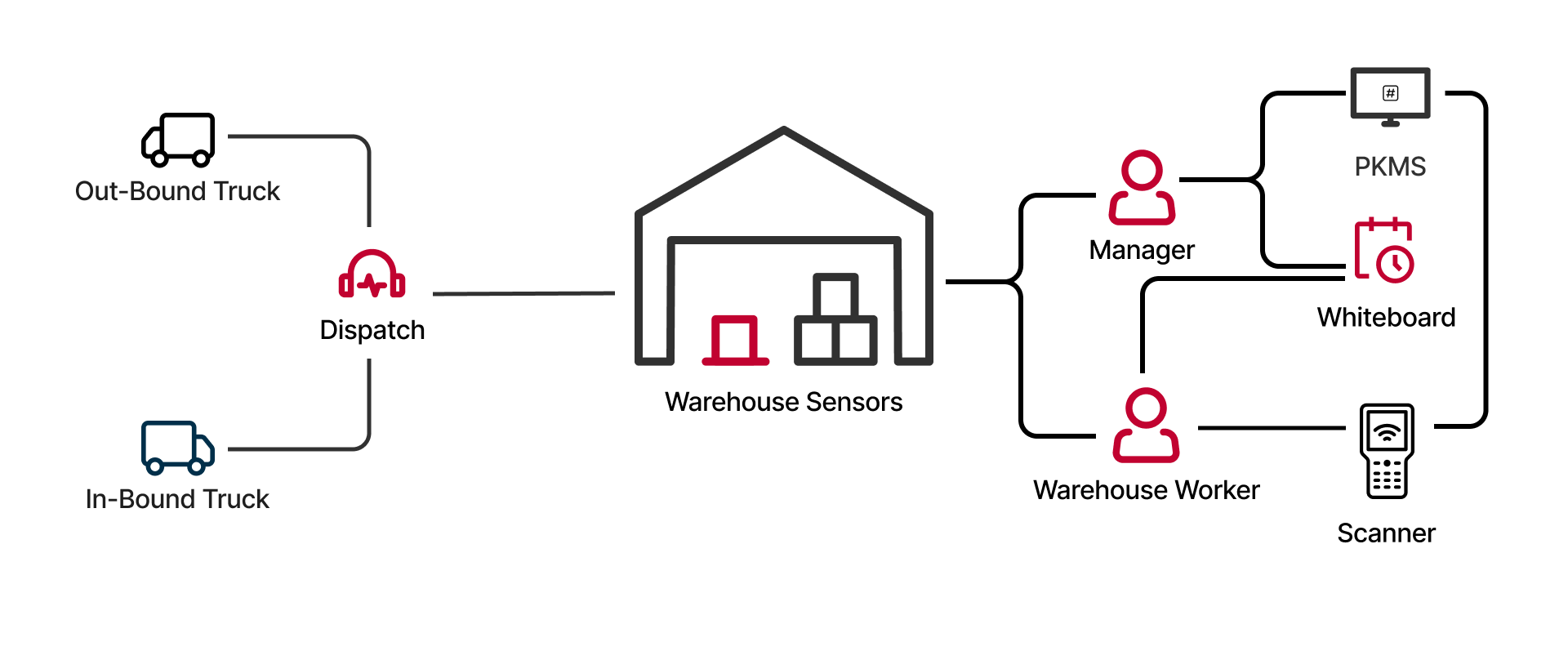
Recommendation 1
Reduce bottlenecks by creating tools that communicates GPS and PKMS information to myQ Scanner for Warehouse Workers.
When the team I were exploring possible tools, we identified that managers need a system to provide codes and update docks without the help of a dispatcher to communicate with truck drivers and workers. Without the help of a dispatcher, managers can reduce bottlenecks and issues with communicating with third-party individuals to operate their facility.
Managers can provide dock information to truck drivers and workers through a GPS Transmitter while tracking their estimated time of arrival to the facility. As a result, warehouse workers can estimate and manage their time staging and loading palettes at each dock appropriately.
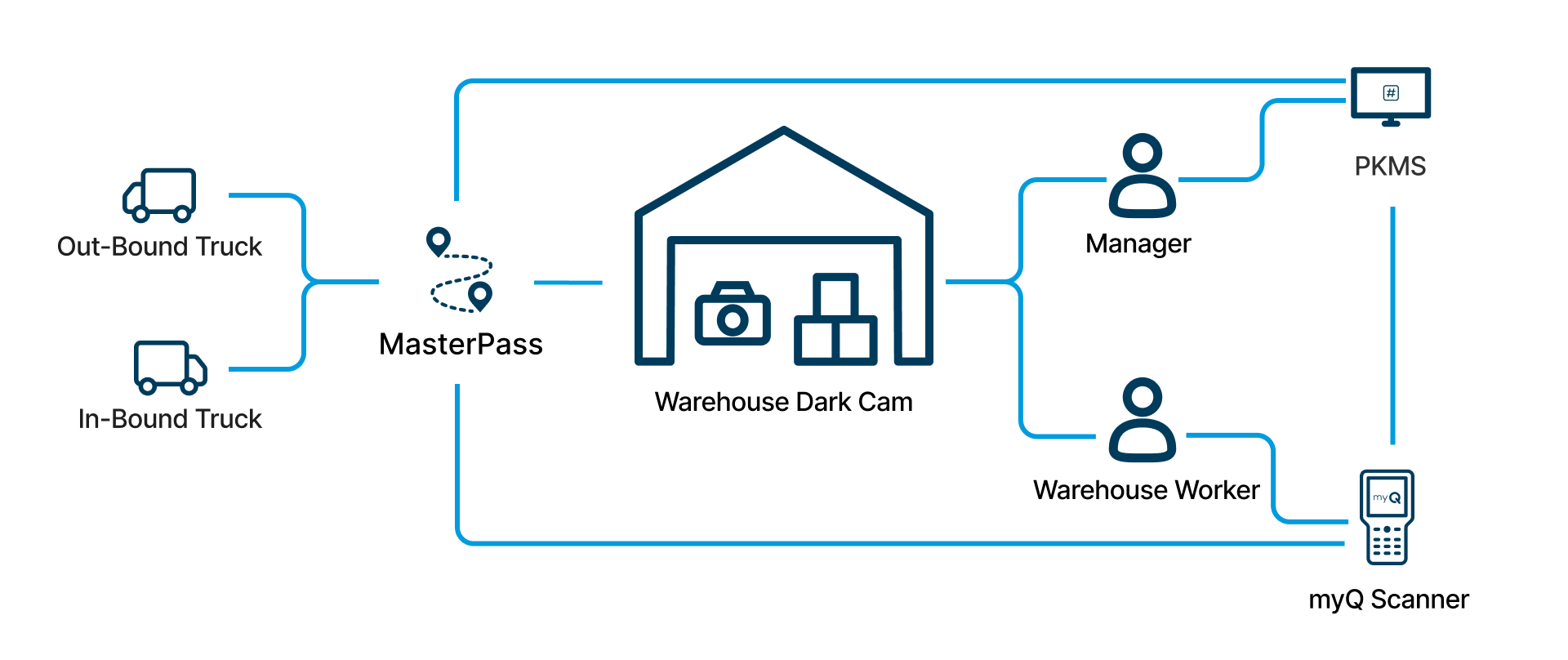
Warehouse workers can anticipate incoming trucks by tracking their location via the MyQ Scanner app. The scanner is an essential tool that workers use to scan palettes. However, our Scanner application will also assist by displaying the truck's arrival time and dock number, allowing for better management of staging and loading.
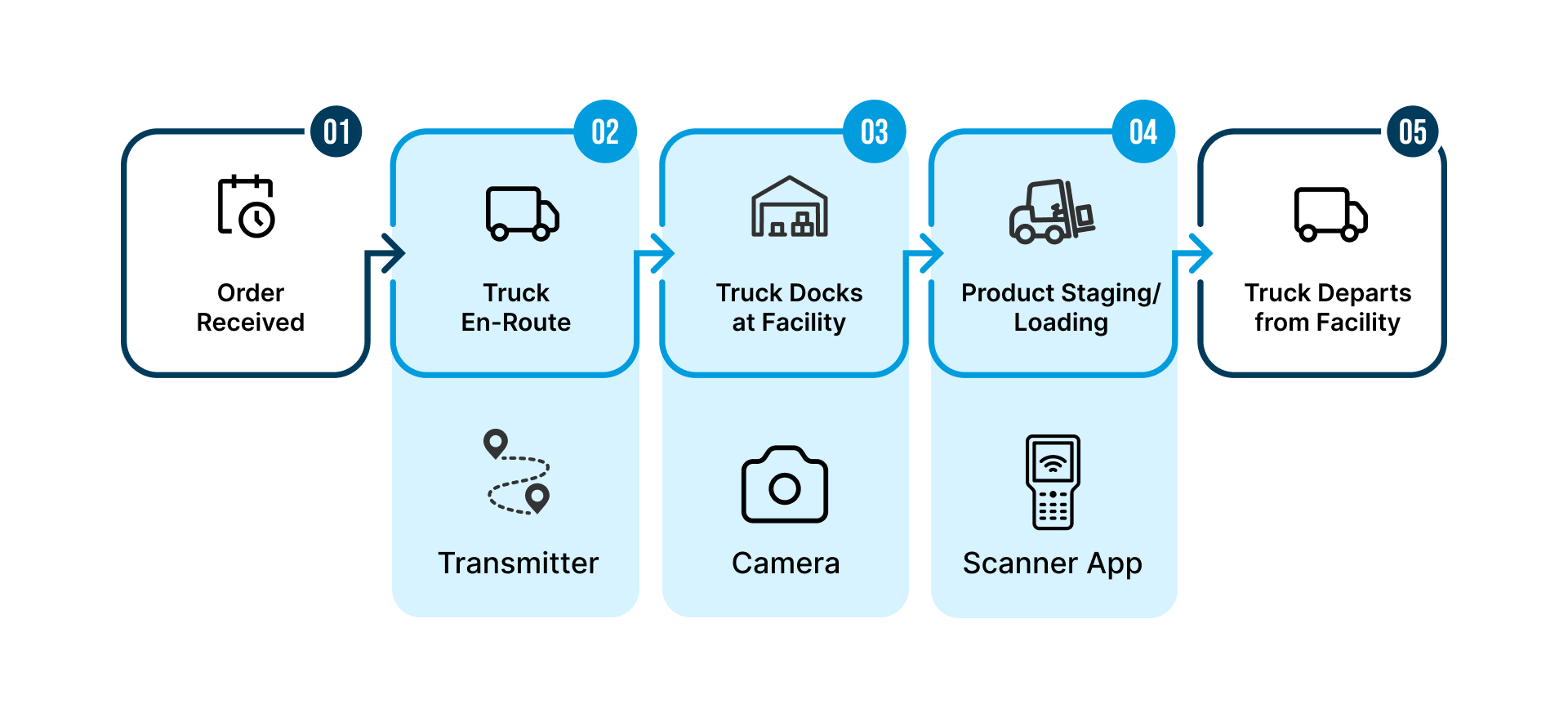
The GPS Transmitter, known as the MasterPass, and AI Camera provide workers with information about drivers' ETAs and the visibility of pallets on the dock. This information is accessible to warehouse workers through the scanner application.
Insight 2
Warehouse workers need visibility on the floor to anticipate incoming trucks
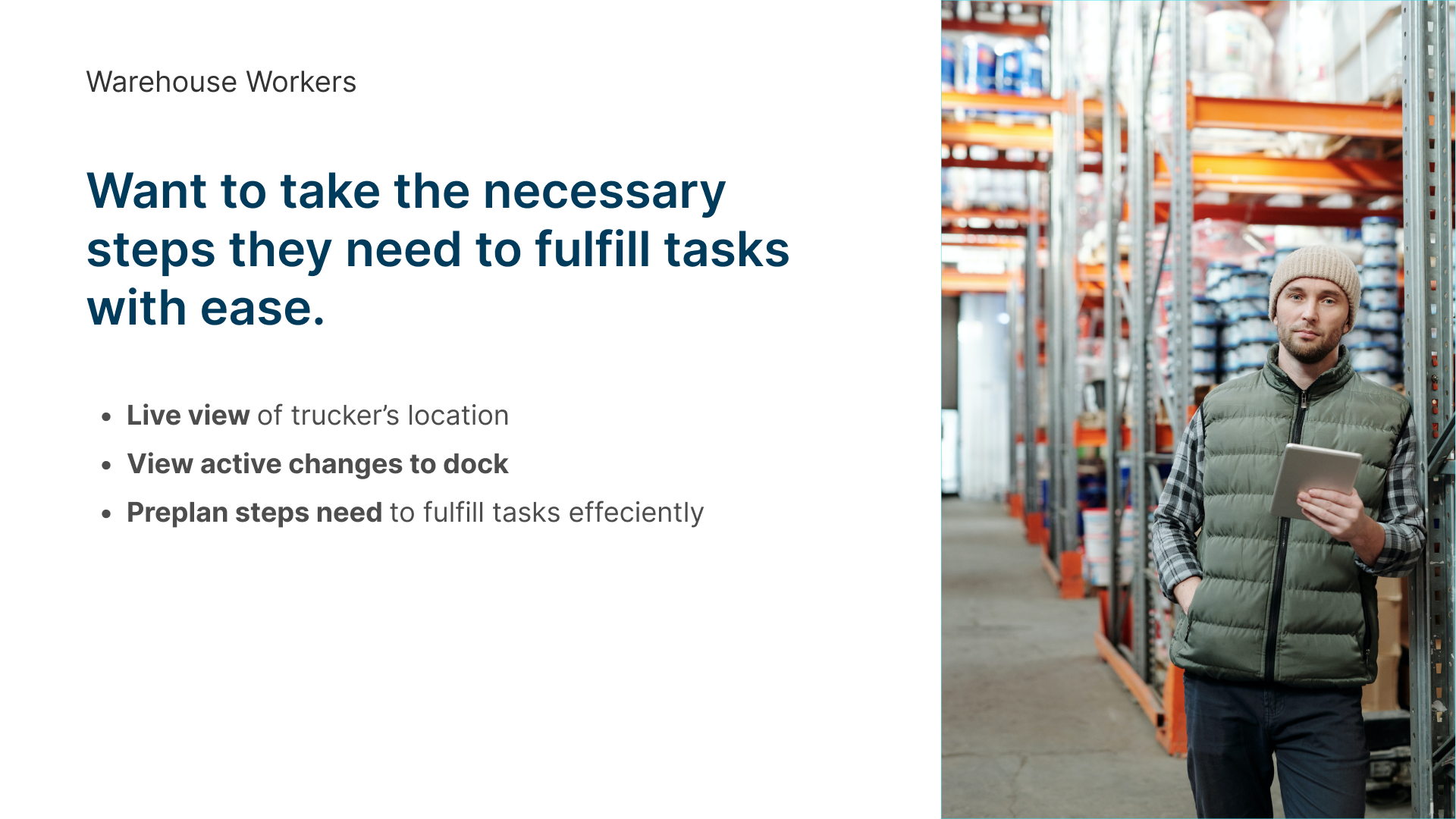
Warehouse workers require real-time visibility on the floor during shipments for several crucial reasons:
01
Efficient resource allocation: With accurate information about incoming trucks and shipments, workers can better plan their tasks and allocate resources appropriately.
02
Reduced wait times: Visibility allows workers to prepare for arrivals, minimizing idle time and speeding up the unloading process.
03
Improved coordination: When workers know what's coming and when, they can coordinate more effectively with colleagues and managers.
04
Enhanced safety: Awareness of incoming traffic helps workers maintain a safe working environment by avoiding potential hazards.
05
Increased productivity: With better visibility, workers can prioritize tasks and manage their workload more efficiently, leading to increased overall productivity.
By providing warehouse workers with real-time visibility of incoming shipments and truck locations, we can significantly improve the efficiency and effectiveness of warehouse operations.
Recommendation 2
Warehouse workers can anticipate incoming shipments via the Scanner application's detailed shipment screen
In the shipment screen, warehouse workers can view the shipment details through the dock schedule, dock details and history.
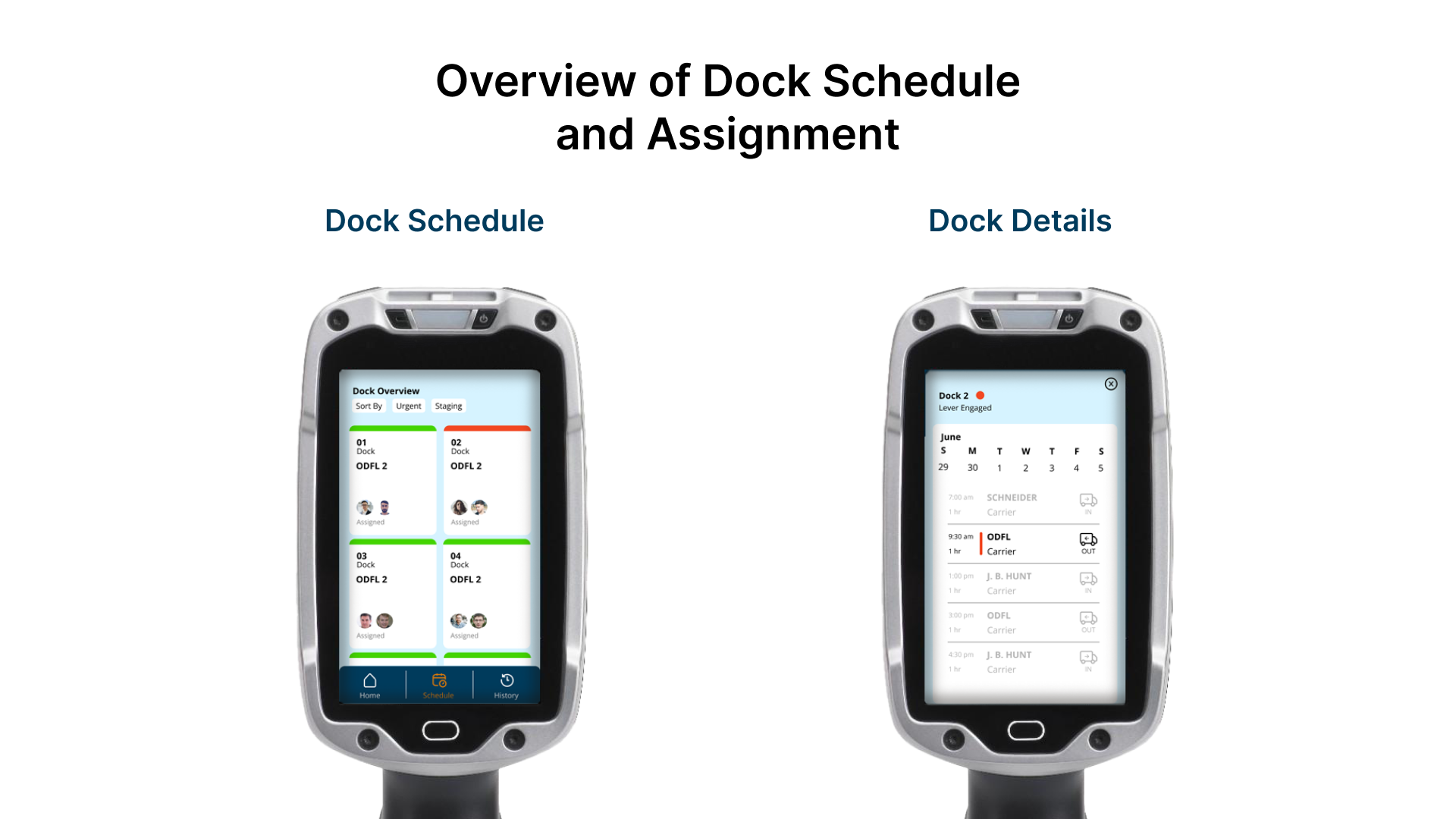
The main goal of the scanner application is to provide warehouse workers with visibility of the floor and shipments. It focuses on the truck's docking system, represented by a red light-green light system. When a truck is docked, this system is activated in the scanner application. Additionally, the dock details display a list of trucks scheduled to dock at specific locations, including their arrival times, carriers, and expected durations. This information helps warehouse workers manage their time more effectively when staging and loading pallets.
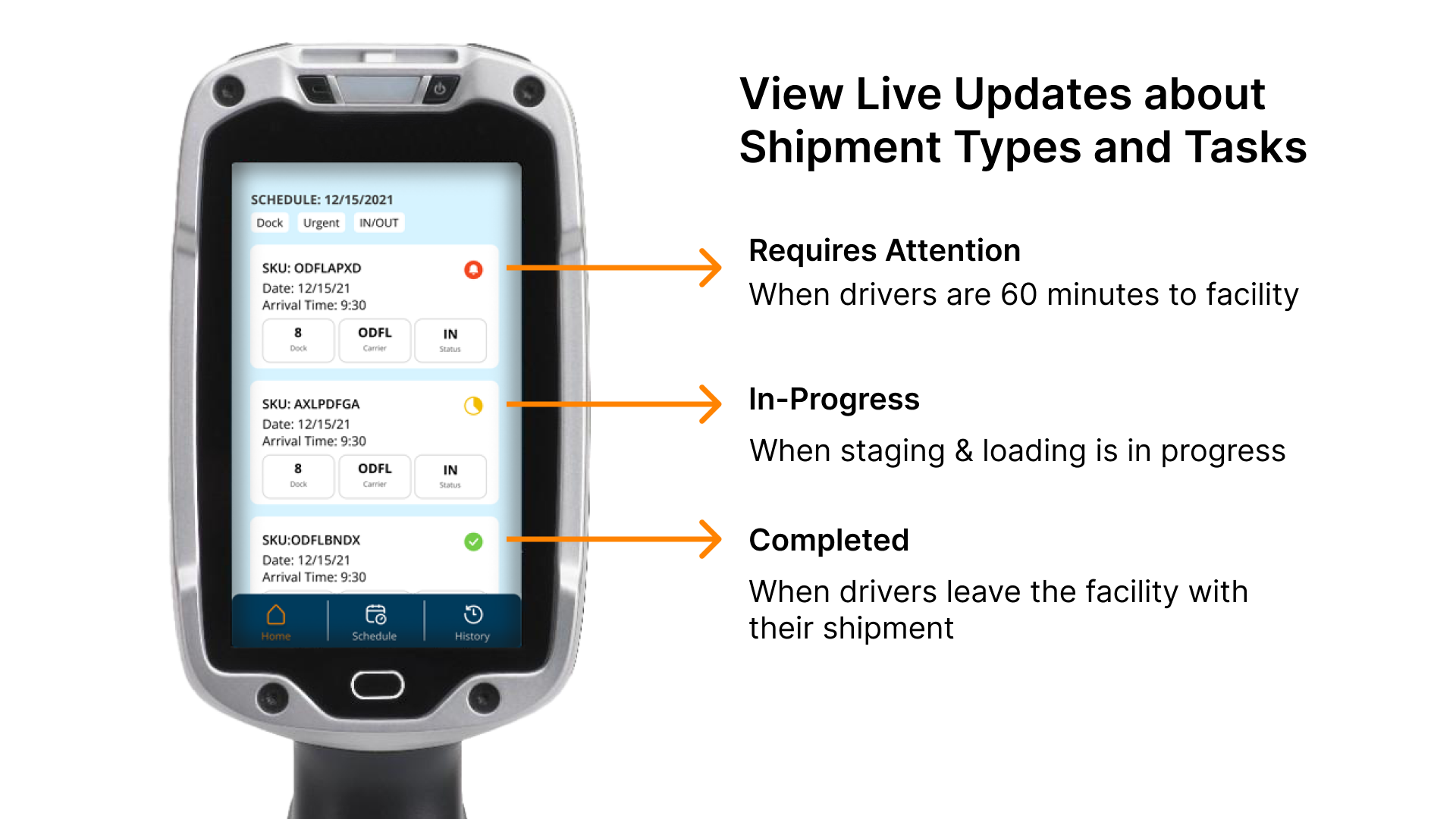
Warehouse workers also have an overview of tasks they need to fulfill showcased in this home screen. Each icon represents time-sensitive tasks they must work on before and during the docking process.
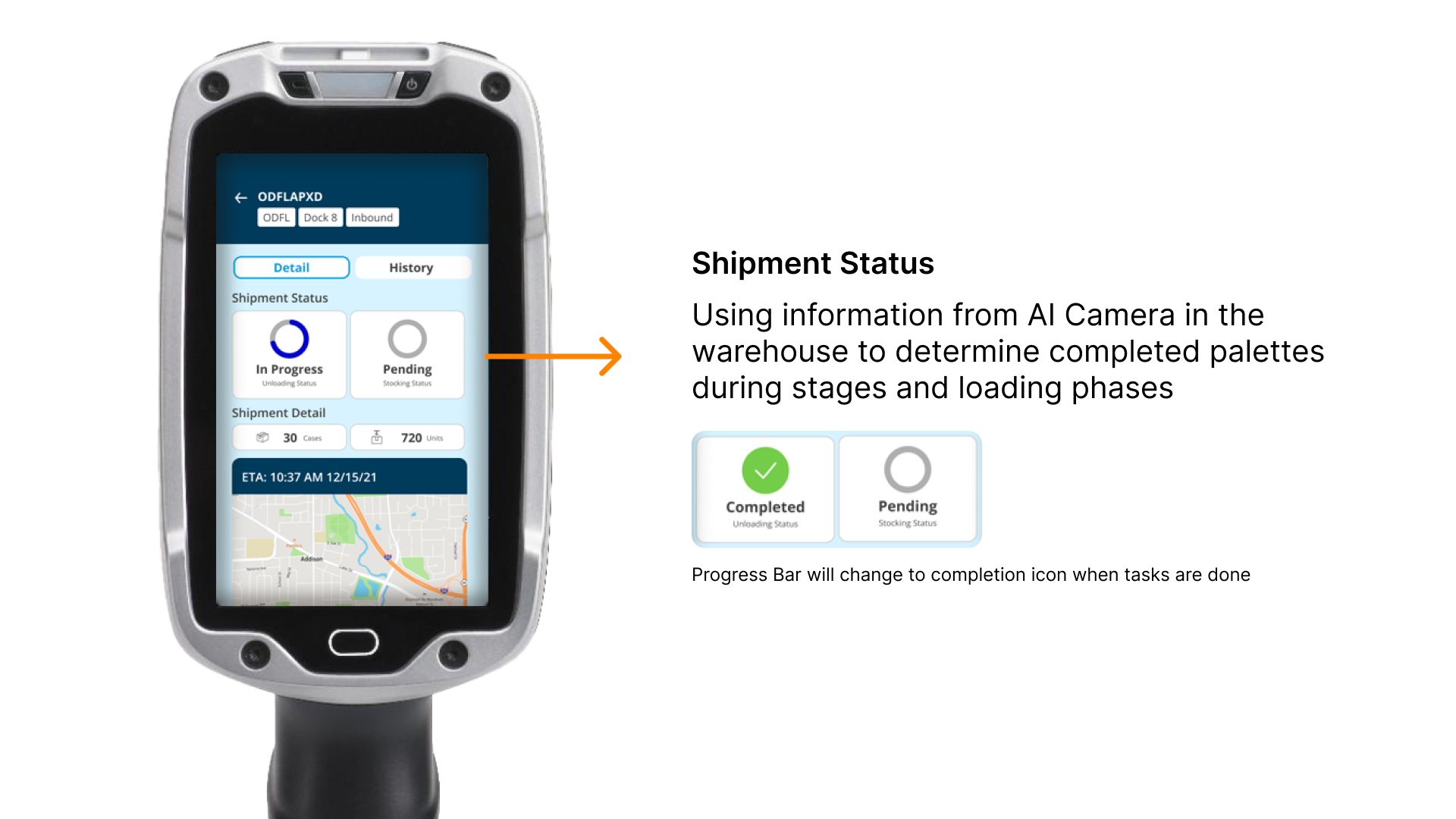
When looking into each detailed shipment, our AI Camera located in the warehouse, looks into the truck's cargo to see how many palettes are needed to complete the task. We were able to identify the number of palettes through machine learning and evaluate the progress of staging and loading/unloading process.
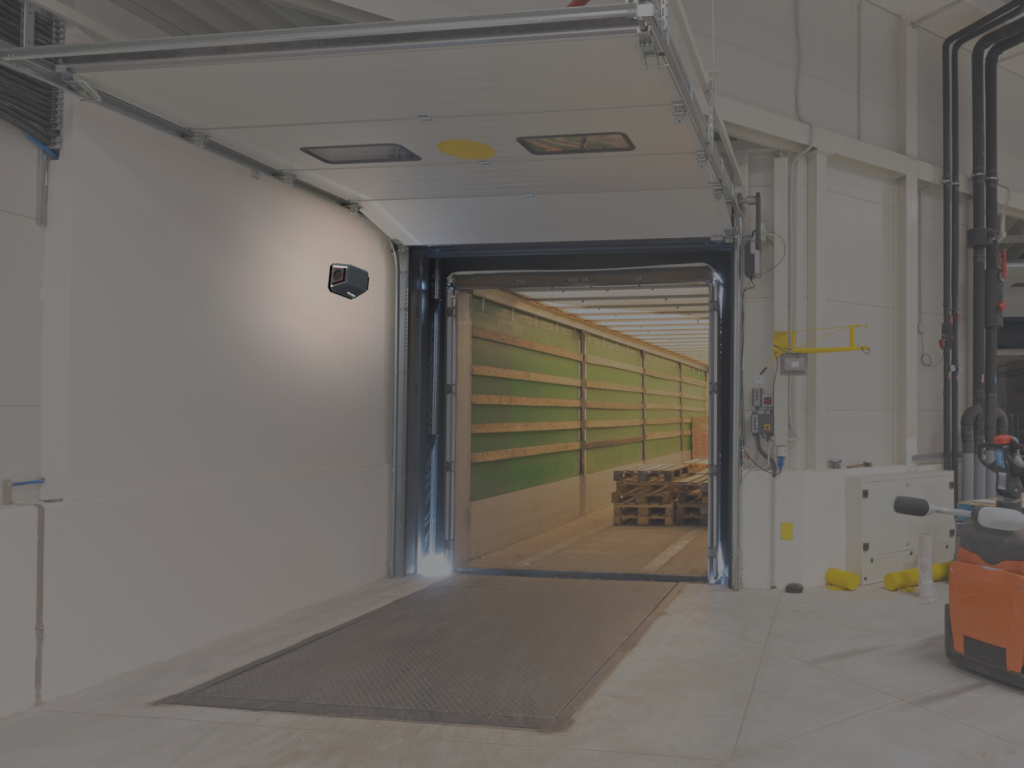
We developed an AI Camera to replace old sensors located on the warehouse floor to help record the truck's status during the docking stage. The AI Camera allows warehouse workers and managers take inventory of any missing palettes that could occur during this stage.
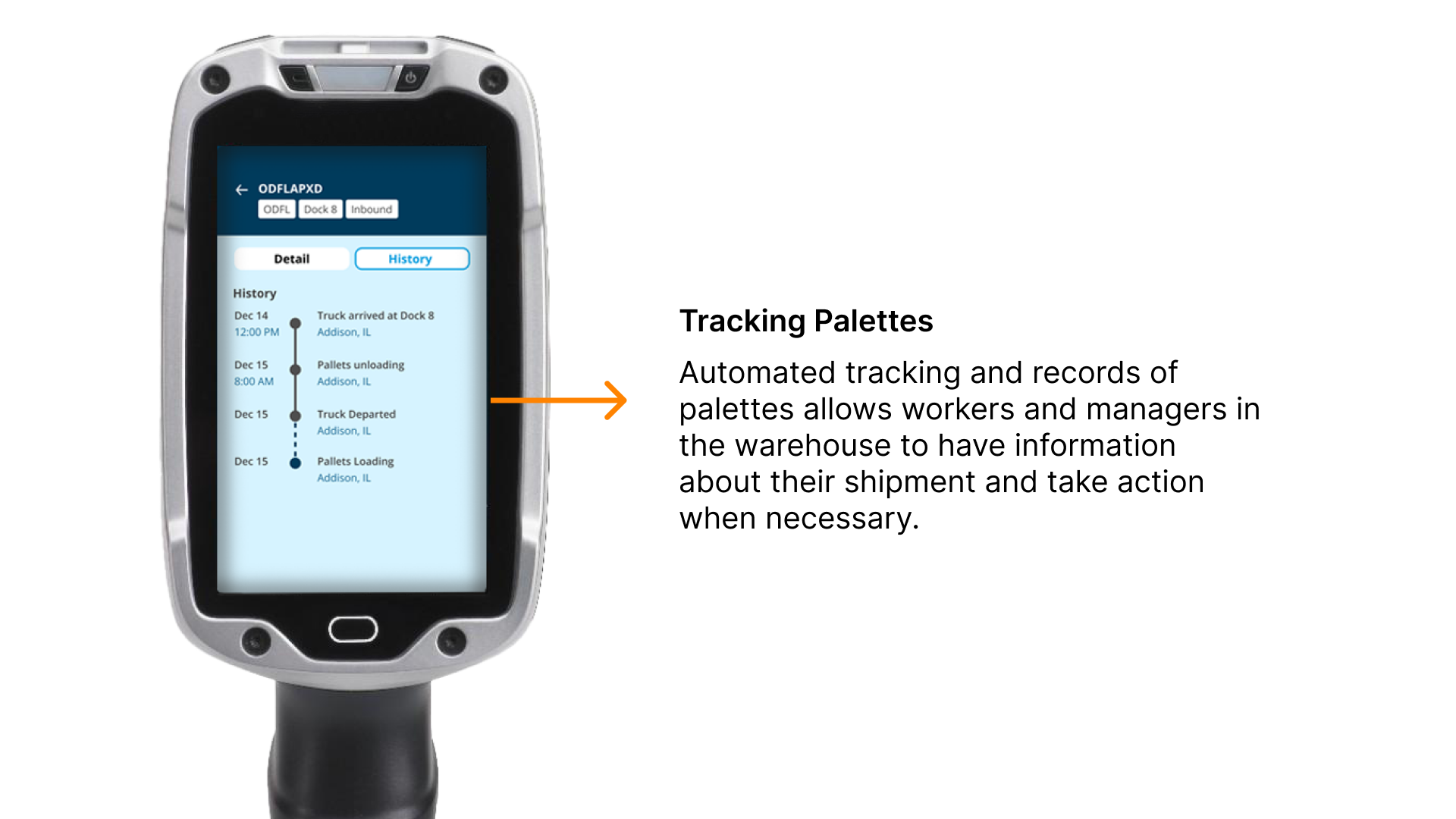
Insight 3
Truck Drivers are unable to communicate with facilities without direct line of communication.
Drivers communicate with dispatchers to view dock numbers, as they do not have a direct line of communication to facilities even within the warehouse area. Therefore, truck drivers would like to view dock numbers and access code without viewing their mobile phones so they can enter the facility with ease
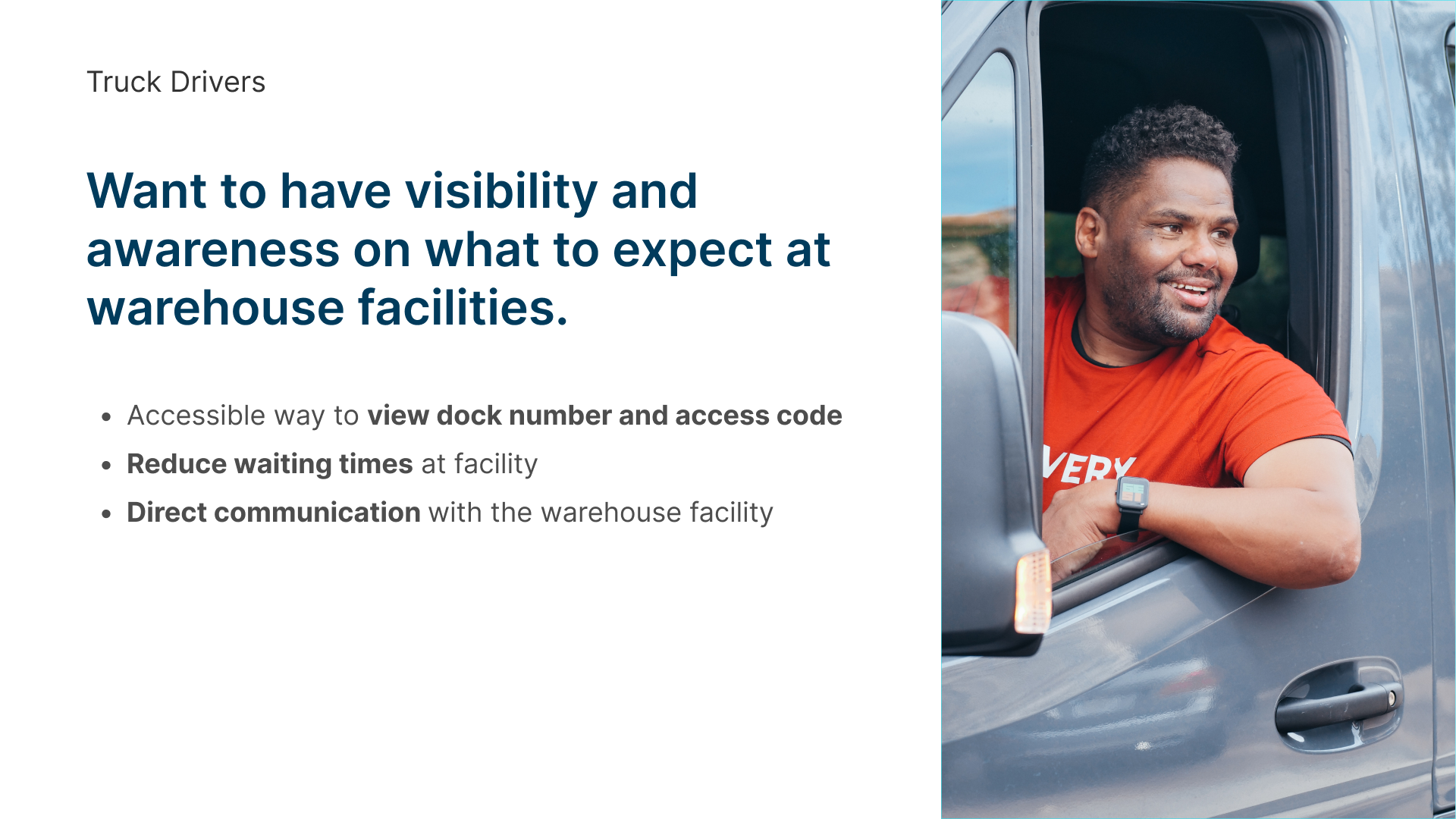
Recommendation 3
Design a GPS transmitter that provides codes and dock number on LED screen
Since the scanner application uses GPS to locate the truck driver, I suggested that the industrial designers incorporate a small LED screen to display codes and dock numbers to reduce bottlenecks in inbound shipments.
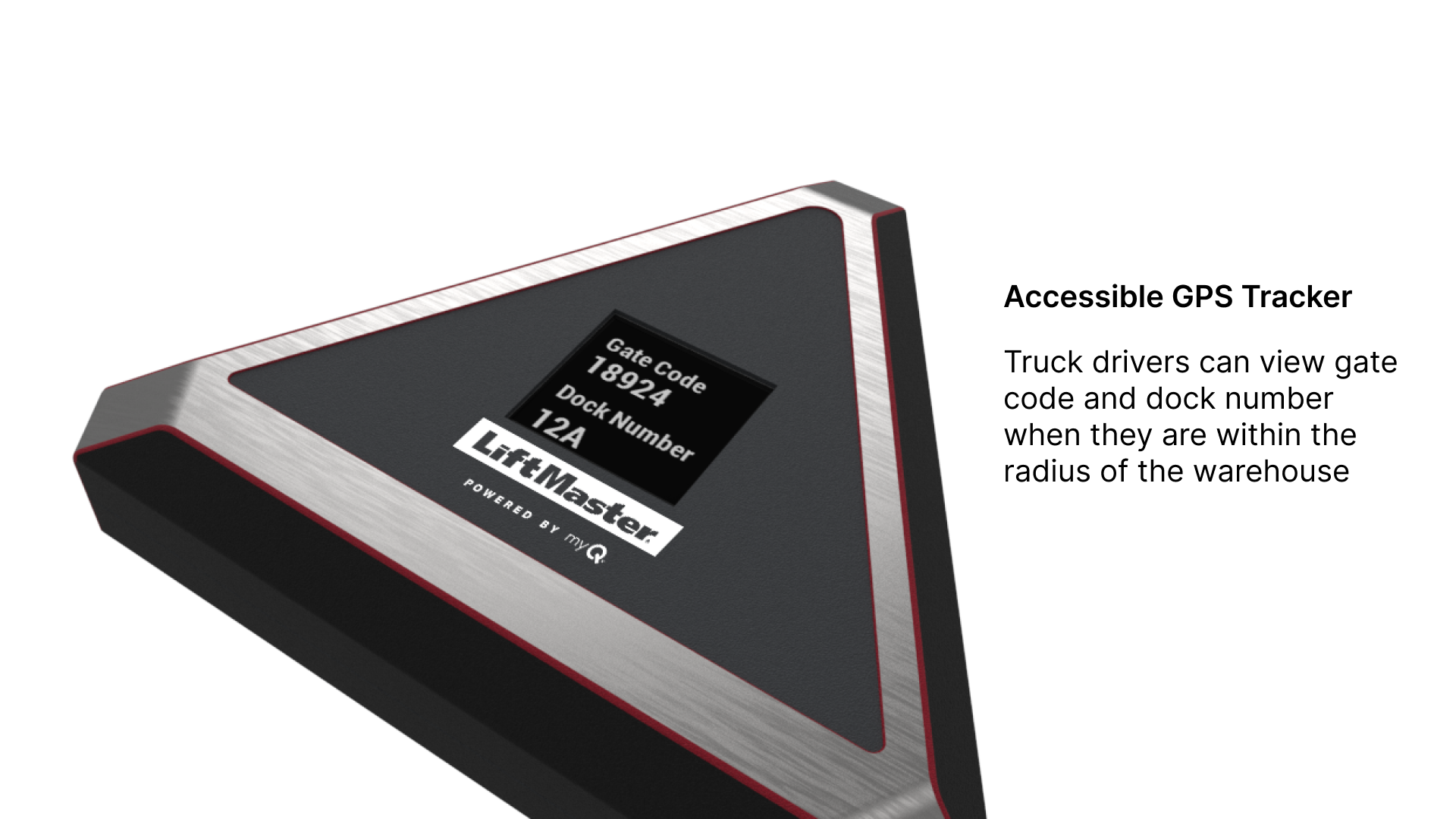
The GPS tracker with an LED screen for truck drivers offers several key benefits:
01
Improved Communication: Drivers can receive dock numbers and access codes directly, eliminating the need for dispatcher intermediaries.
02
Reduced Wait Times: Quick access to facility information allows drivers to proceed to their designated areas without delays.
03
Enhanced Safety: Drivers can view important information without using their mobile phones while driving.
04
Increased Efficiency: Streamlined entry process reduces bottlenecks at facility entrances.
05
Real-time Updates: The LED screen can display changes in dock assignments or other important notifications instantly.
By providing crucial information at a glance, this GPS tracker significantly improves the driver's experience and contributes to overall operational efficiency.
Outcomes
After working on this project, my team and I presented our work to the CEO and VPs of Chamberlain Group. We received positive feedback from leadership as we reimagined what we could do to improve warehouse communication and tracking.
01
Time-Saving: The myQ Scanner App can save up to 3 hours per day during the loading and staging process.
02
Warehouse Optimization: The myQ Scanner app enables more efficient use of floor time with reduced labor requirements.
03
Reduced Detention Fees: Warehouses incur $85+ per hour for shipping delays at the facility while undocked. On average, facilities lose $1,280 annually per truck in detention fees.
Learnings
Throughout this project, I gained valuable skills and experiences while collaborating with diverse users to create an integrated product system. It was particularly enlightening to develop a system that combines physical and digital components, prompting me to consider the relationship between hardware and software.
Working on hardware and software products
Through my UXR experience, I applied my knowledge to both hardware and software products to help increase communication and tracking within the warehouse. Although I didn't directly designed the hardware products, my suggestions and UXR experience helped my team understand the user's needs and created products that benefits the three types of users.
More user testing for further improvements
Given the time-restraint we had during the internship, I wished I could conduct more user testing. However given the complexity and scale of warehouse facilities, it would require more time and funds to conduct this scale of testing.